My barely 3-year-old Presonus Eris 3.5 monitors have started making crackling, popping, and hissing noises—depending on their mood!
Two capacitors have gone bad, and the local distributor asked for $200 for the repair, whereas a new pair nowadays costs only $100.
The distributor in a neighbouring country mentioned that there’s no service available for these monitors, claiming they are ‘commercially developed in a production line,’ although the meaning behind that statement is a bit unclear to me.
It seems they might be suggesting that these monitors are mass-produced and not designed for individual repair or servicing. I don’t see how that can be the case, but let’s move along, like obedient citizens in a world of placebo abundance 😀
If you’re facing a similar problem and have access to a soldering iron (or know someone who does :P), consider replacing the two brown capacitors with 24v 1000μF ones, or any other bulging in the cap ones that seem suspect. Good new parts are available everywhere nowadays and cost less than 50cents each…
The problematic capacitors in my case were the bulging brown ones marked with the purple arrows in the following image.
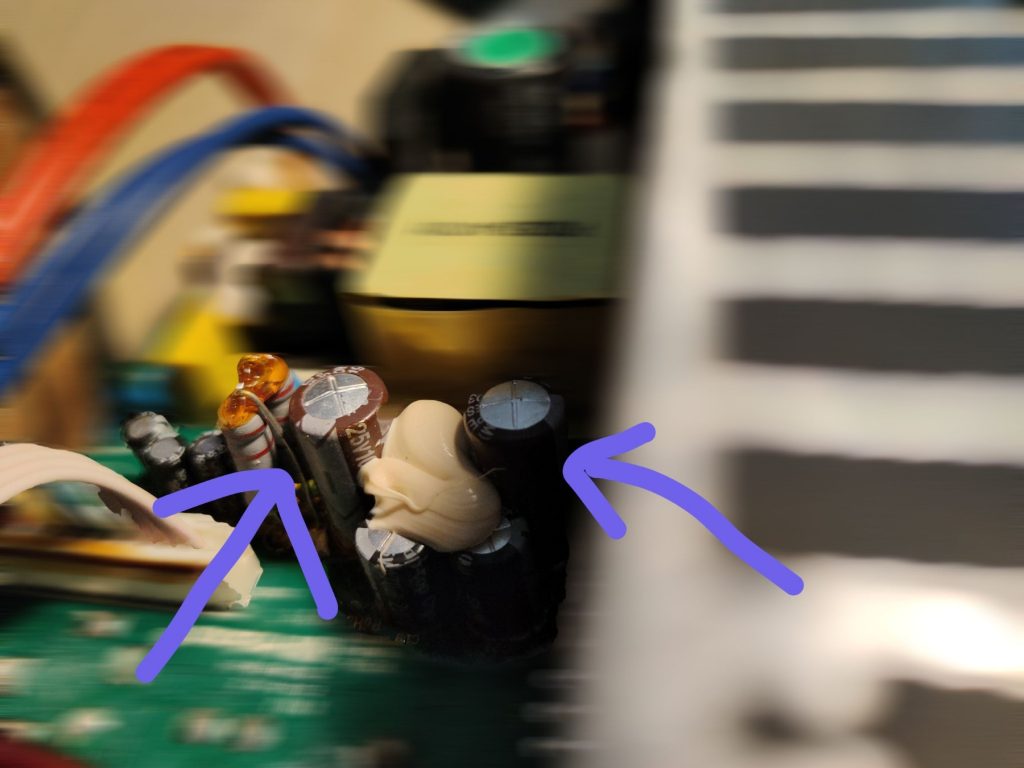
Needless to say, if you decide to tackle the project, do so at your own risk. The circuit involves a high current mains side, so take all necessary precautions to protect yourself.
Have a good one!